The Biggest Issue With Modular Buildings Containers, And How You Can Fix It
Modular Buildings Containers
Modular buildings containers are designed to meet the unique requirements of every project. They can be built in a factory and then delivered to the site to be installed. This can reduce the amount of time required to finish an entire building, and also reduces waste.
They can be used to build many different structures like hospitals and offices. They have been used successfully to address a range of problems, including housing shortages during the pandemic.
Cost-Effectiveness
Modular structures are a cost-effective solution to many business requirements. The buildings are built off-site, then constructed on site and save money on labor costs. Modular construction can help companies cut costs by reducing waste. It also reduces construction workers required on the job and allows a quicker completion of the project.
The modular construction method is faster and safer than traditional methods. It also prevents delays due to weather and other factors. It also lowers the risk of mechanic's liens which could occur when contractors are not paid for their work. It is also easier for companies to obtain financing and are able to meet their deadlines more efficiently.
The most popular building block for modular structures are shipping containers. 30ft Shipping Containers come in a variety of sizes and are modified to meet the specific needs of each project. They can be fitted out with windows, HVAC units and insulation, making them ideal for both homes and offices. They can also be transported, making them an excellent choice for projects that require frequent relocation.
Another benefit of modular building containers is that they can be used in any climate. The manufacturing process ensures that the structure is well-insulated, and also has extra structural strength to withstand harsh conditions. This means that the structure will be more able to withstand extreme cold and heat, and it will also have better fire resistance.
Additionally, altering shipping containers is a greener option than traditional construction. The materials used in the modification process are recycled and recycled, reducing the demand for new resources. This method reduces waste and is in line both with corporate social responsibility objectives and sustainability.
Inconsistency between manufacturers can be a problem when it comes to modular buildings. These structures are custom-made and therefore it is essential that buyers conduct a thorough search before deciding on a supplier. This will allow buyers to avoid issues such as inadequate workmanship or a flawed design. In addition, it is essential to communicate with the manufacturer throughout the process. This will ensure all parties are aware and can adjust the schedule as necessary.
Flexibility
Modular construction is a popular alternative to traditional building methods. It is able to reduce the time required for construction, save money and provide an earlier turnaround than traditional methods. It is also eco-friendly and sustainable, using recycled materials and avoiding wastage. This method is particularly useful for moving equipment or workers around a site. It can be utilized in a variety of ways.
Containerized modular buildings are built from shipping containers that have been joined vertically or horizontally. They can be used for office space, clinics, and dormitories, among other things. The containers can be arranged to meet your requirements, and they are delivered to the construction site in good condition for use. These structures are easy to build and designed to withstand harsh conditions. They can be easily moved and reused, which reduces the need for building additional structures on the site.
Shipping container modular building is an increasing trend in the construction industry. It offers cost-effectiveness and flexibility, in addition to sustainability. Many companies are now using this technique to build everything from food trucks to office buildings. However, this method is still relatively new and requires careful planning and preparation. The primary challenge is to ensure that the design meets the necessary requirements and is solid in structure.
The modular construction method permits a quicker turnaround and is less disruptive than traditional construction methods. The modules can be delivered from the factory to the construction site in flatpack forms or as profiles, and are constructed on-site by skilled technicians. This technique can also cut down on the need for foundation and excavation work, allowing constructions to move faster.
By adding insulation and HVAC units, as well as windows to a shipping container, it can be converted into a modular office. The result is a spacious and comfortable workplace that is flooded with plenty of light. Moreover the container can be powder-coated with corporate colors to create an eye-catching and attractive exterior. This will help brand the building and draw customers. The flexibility of shipping containers makes it an ideal choice for offices, retail pop-up shops and exhibit booths.
Durability
The strength of modular building containers makes them a great choice for housing and offices. They are able to be used in tough conditions with high seismic activity and high winds. They are also resistant to flooding and can be elevated on stilts or concrete foundations to stop water damage. They can also be customizable, with a broad selection of door, window, and insulation options.
These structures are also easy to maintain and clean. Modular construction has a shorter build time than traditional methods, and the prefabrication process is carried out in a controlled space. Since they do not have roof shingles, there are no worries about termite infestations or other bugs. Steel construction makes them more durable than traditional buildings.
Modular shipping containers are now a popular choice for construction due to their low cost and durability. They can be used as living spaces, office spaces and even mobile schools. They can be stacked together to create large buildings or used as single-use units. Since they are constructed from prefabricated components, modular buildings can be built to suit specific needs.
Modular construction has many advantages, including cost and schedule savings. It also improves the safety of workers and improves working conditions. They are also great for remote areas, where traditional builders and materials are difficult to locate. However, there are 20ft Shipping Containers of using modular construction for construction projects. It might not be appropriate in some projects, such as commercial and residential construction.
Additionally, some companies that offer modular construction services may provide low-quality modules that deteriorate quickly. It is crucial to select a business that makes use of high-quality materials and has a wealth of experience in the field. This will ensure the top quality of your modular building as well as its durability.
Shipping container modular construction is a novel method of building. By converting old shipping containers into office space businesses can cut costs and gain a competitive advantage on the market. Despite these challenges, modular construction has gained significant support from engineers and architects.
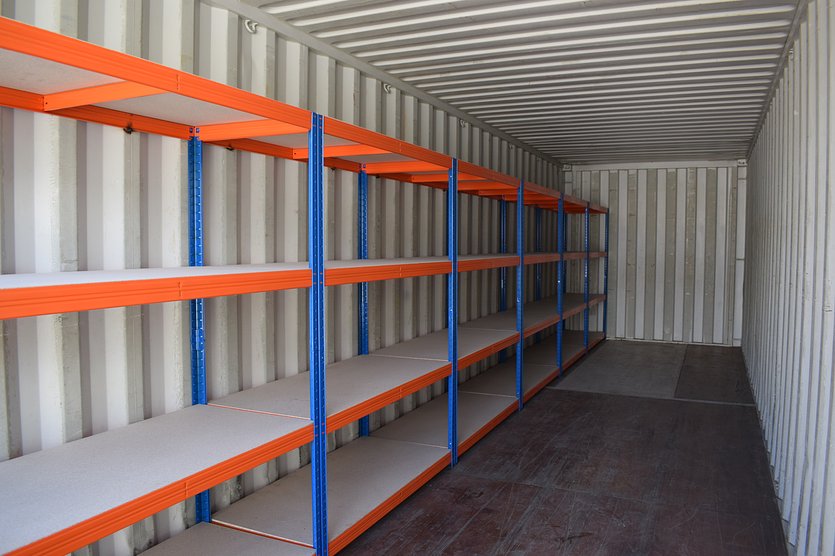
Sustainability
Modular buildings are sustainable and demonstrate how intelligent design can aid global efforts to safeguard the environment. They use prefabricated parts and are built in factories which reduces waste, saves energy and speeds up the building process. The modular construction method is also flexible and cost-effective, making it ideal for a variety of needs.
Modular construction consists of the assembling of standard shipping containers to build offices, kindergartens, schools and other facilities. The design of the building is based on the needs of the customer's requirements and incorporates partition walls and windows as well as electrical and plumbing components. The modules are transported to the building site in flatpack form or as profiles, and then assembled by skilled technicians. The modules are then joined together on site, and finished with ceilings, walls, and flooring.
A major advantage of modular buildings is that the majority of work is performed in a factory. This means that there is no need to hire expensive construction workers and large equipment to complete the job. This means that construction is performed in a controlled setting, with minimal disturbance to the surrounding landscape.
Another way that modular buildings are green is through the use of recycled materials, such as wood and steel as well as repurposed shipping containers. These containers would have remained at ports if they were not transformed into modular structures.
The reduction of carbon dioxide emissions is one of the most important aspects to sustainability. Traditional construction processes employ large machines and creates a lot waste, which contributes towards the global carbon footprint. Modular buildings are typically built in factories and emit much less carbon dioxide than traditional construction methods.
Modular construction can be an ideal option for businesses who need to expand their offices or relocate their offices. This building method is flexible and can be easily rearranged or altered. The structures can be moved easily without having to tear them down which means that there is less requirement for raw materials. Modular structures can be easily altered by removing or adding standard components. This can help businesses reduce their energy usage and even make them eligible for LEED Certification.